Estimate 3D Print Time
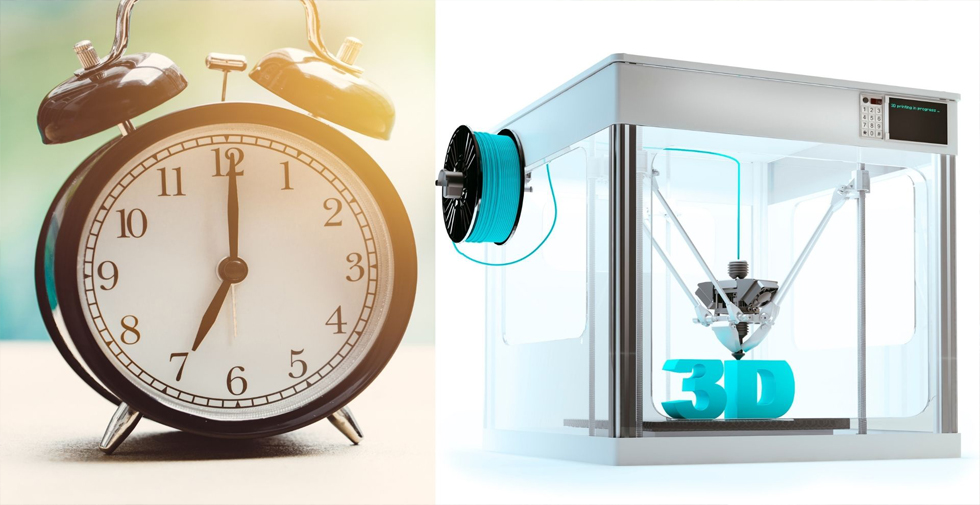
While 3D printing has many advantages, it is not able to provide a fast turnaround time. It takes more time to build a layer upon layer than it does to cut a design from a single piece. This should be taken into consideration when developing a manufacturing process using 3D printing technology.
Here are some ways to estimate the printing time of a particular 3D model. These methods are estimates only and may not be accurate.
Method 1: Using your slicer
The most convenient option would be to rely on the estimate given by your Slicer software. This feature may not be available in all slicers. You should be okay with brands such as Cura or Simplify3D. This is a great method to adjust your slicer settings to see how they affect the estimated printing times. You may want to balance the printing time and detail precision by playing with layer height settings. This instant feedback mechanism can be very useful during the initial stages.
Method 2: Estimate using G-Code
Slicers will not look at the 3D model when estimating the time for 3D printing. The Gcode is much more important. G-Code is the 3D printer’s “machine language”. It is composed of commands the 3D printer must follow. G-Codes are generated by the slicer based on the 3D model source and any slicer settings. The G-Code contains information about printing parameters, such as layer height and printing speed, temperature, bed temperature, and printing temperature. Slicers that estimate printing time can also use the G-Code reference. Online tools are available if your slicer doesn’t have this function. It will first estimate the parameters of your model by uploading it to the site. This G-Code analyzer doesn’t take into consideration the model of your 3D printer. This website has a larger margin of error when estimating printing times. For larger prints, the margin of error can be as high as 40% to 60%..
Which factors influence 3D printing time?
In most cases, a shorter printing time is ideal. You don’t use as much power and you don’t have to keep watch over the project for too long. More importantly, this means that you can print more projects within the same period. For these reasons, shaving off even just a few minutes of printing time is worth the effort.
This is the importance of using a good 3D printing time estimator. By making a few changes in printing parameters, you can massively boost the productivity of your 3D printer. However, knowing which settings to change is also as important.
If you want to reduce the printing time for your project, here are some changes you can consider making:
1. Increase layer width
Increasing the layer width could be the single biggest change you can make to your slicer settings if you want to reduce the printing time. Printing each layer thicker means that your model can be printed with a lower number of layers.
There are some drawbacks to this method, of course. If your model has fine details, you might lose out on detail precision because of the thicker layers. You may also need to swap your stock nozzle for one with a larger diameter. The general rule of thumb is that the layer width must be maintained at around 80% of the nozzle diameter. Otherwise, you may end up running into layer adhesion issues.
2. Reduce infill density
The 3D printing shell contains the infill. This adds weight and mechanical support to the final product. The infill is essential but can be reduced to reduce filament usage and print time. This reduces the mechanical strength and makes it a great solution for projects that don’t require weight bearing. The infill density can vary from 0% to 100 percent. A value of 20% to 35% is sufficient for most projects. For more heavy-duty applications, this can be increased to 50%. Although an increase infill density of 50% or more is beneficial, the marginal benefits are less.
3. Reduce shell thickness
The shell is the outer layer of a 3D printed object. The shell gives a 3D printer mechanical strength and stability, just like its infill. Multiples of the diameter of the nozzle determine the thickness of the shell. To increase the shell thickness, the nozzle simply passes around the perimeter of the 3D printer. Most cases, the shell thickness can be adjusted to fit the nozzle diameter at two- or three times its maximum. For more demanding applications, this can be increased to four- or five times the nozzle diameter. A single layer of shell thickness reduction will make a big difference in the printing time.
4. Reducing supports
3D printing is not without its challenges. They are necessary to ensure that any overhanging parts do not fall, as their name suggests. This is a must-have when printing complex designs. While they are essential for many projects, you can reduce the number of support structures needed. This will reduce the printing time and also save filament. There are many ways to reduce support structures. The easiest way is to reorient your model. To ensure that your model can self-reinforce, the goal is to keep any overhanging elements at or below 45 degrees of inclines. Reduced supports will also reduce the amount of filament you print and the amount required for post-processing.
Final thoughts
3D printing is a complex process, especially for commercial users. This affects the speed of the process and how much power 3D printing uses. It’s easy to estimate the time it will take to print 3D models. It doesn’t matter if you use your local slicer software or an internet tool to estimate the printing time, it can still be useful in planning. These estimates are only estimates and may be incomplete. Some calibration is necessary.